PROCESSO DE FABRICAÇÃO DE DISPOSITIVOS MÉDICOS POR INJEÇÃO PLÁSTICA.
A Moldagem por Injeção consiste na injeção, sob condições de alta pressão, de materiais amolecidos induzidos por calor em uma cavidade de molde onde são modelados. As vantagens que o processo pode oferecer no desenvolvimento de medicamentos dizem respeito tanto aos custos de produção, quanto às características tecnológicas / biofarmacêuticas dos itens moldados.
Os principais determinantes do sucesso desta técnica na área farmacêutica estão relacionados à sua escalabilidade e patenteabilidade. Na verdade, a Moldagem por injeção é um processo cíclico potencialmente automatizado que pode ser facilmente transferido para a escala industrial pelo uso de equipamentos e moldes maiores. Um único ciclo de injeção pode durar poucos segundos e, em muitos casos, os moldes até possibilitam a produção simultânea de mais de uma unidade, auxiliando na redução do tempo de processo.
Além disso, as condições do processo tipicamente envolvidas, pressão e calor, reduzem a contaminação microbiana (autosterilização) e promovem interações fármaco-polímero com a possível formação de soluções sólidas ou dispersões. Como na técnica de Hot Melt Extrusion (HME), isso aumentaria a taxa de dissolução e, possivelmente, melhoraria a biodisponibilidade de drogas pouco solúveis.
O grande potencial da molagem por injeção para a produção de sistemas de liberação de medicamentos é demonstrado pela multiplicidade de patentes depositadas nos últimos dez anos, embora o número de produtos em estágio de desenvolvimento avançado ou já no mercado ainda seja limitado, portanto, ainda há espaço para melhorias e investigações [1].
Como funciona
A Moldagem por Injeção (MI) é uma técnica de fabricação rápida e versátil utilizada na indústria de plásticos para produzir objetos com diferentes tamanhos, formas e, se necessário, muitos detalhes [1]. O processo de MI é realizado em equipamentos apropriados que geralmente consistem em duas partes: a unidade de plastificação/injeção e a unidade de fechamento (Figura 1) [2].
O elemento terminal da máquina de injeção é o molde. É geralmente composto de duas metades que se combinam para formar uma cavidade definida de forma 3D que forma as superfícies externas do objeto moldado. Também é possível projetar moldes com várias cavidades para produzir, dentro de um mesmo ciclo, mais de uma unidade. Uma parte do molde é montada em uma placa fixa, enquanto a outra é móvel, permitindo assim que as duas metades sejam combinadas (molde fechado) ou desacopladas (molde aberto). A unidade de fixação mantém o molde fechado durante a injeção. É necessária uma força de fechamento que exceda a pressão de injeção para evitar que o molde se abra enquanto o material está sendo injetado e para reter a pressão da cavidade. A temperatura do molde é controlada por um sistema de resfriamento que normalmente utiliza água como fluido circulante. Após a injeção, o fundido resfria no molde e, quando suficientemente solidificado, pode ser ejetado por pinos localizados na metade móvel do molde [1].

Figura 1 – Máquina injetora de termoplásticos. Fonte: HARADA (2004).
A Moldagem por injeção é um processo cíclico e possui estágios [3] (figura 2). Ciclo de injeção é o intervalo total de tempo entre o instante em que o molde se fecha durante um ciclo e o período correspondente em que ele se encerra no ciclo seguinte. O ciclo da máquina é a soma do tempo para injeção, do tempo para resfriar a peça injetada, e do tempo de abertura e fechamento do molde [2].
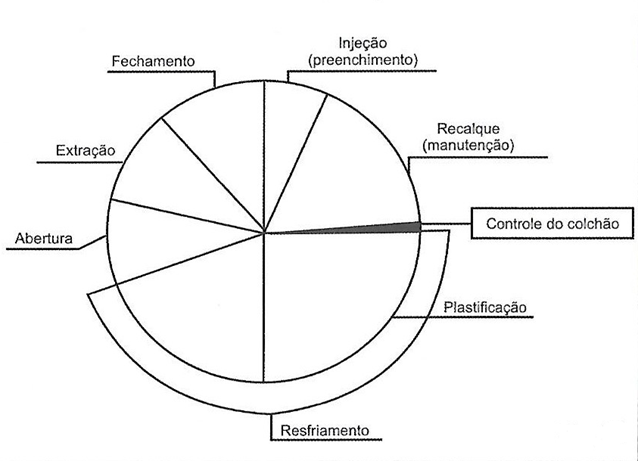
Figura 2 – Ciclo básico de uma máquina injetora. Fonte: Adaptada de FERNANDES et al (2016).
- Temperatura da massa plástica: Para que o polímero preencha a cavidade do molde é necessário que sua viscosidade seja reduzida até um valor ideal, determinado pelas dimensões dos canais de injeção, espessura da peça, e pressão disponível. Esta diminuição de viscosidade é obtida através do aumento no calor transmitido ao polímero diretamente pelas resistências de aquecimento do cilindro.
- Pressão de injeção: é a pressão com que o material é injetado no molde. A pressão de injeção a ser adotada depende da espessura de seção da moldagem e da facilidade de fluxo do material usado.
- Pressão de recalque: é a pressão que atua dentro do tempo de recalque. Essa operação é realizada no processo de moldagem plástica para garantir que todas as cavidades do molde sejam completamente preenchidas.
- Velocidade de rotação do parafuso: influencia a temperatura de massa devido o atrito. Quanto maior for seu valor, maior será a velocidade de escoamento do material pela cavidade, consequentemente, maior a taxa de cisalhamento.
- Temperatura do cilindro de aquecimento: influencia na temperatura da massa. As zonas de aquecimento do cilindro servem para controlar a temperatura, sendo compostas de resistências elétricas que fornecem calor para compensar as perdas de calor do cilindro para o ambiente.
Polímeros mais utilizados em dispositivos médicos
Por causa da ampla gama de polímeros disponíveis, os componentes básicos podem ser escolhidos levando-se em consideração diversos aspectos, como o equipamento, o tempo e os custos do processo, bem como as características que os produtos moldados devem apresentar em função de sua aplicação final. Uma melhoria nas características do produto pode envolver o uso de componentes extras, às vezes muito caros e/ou com processabilidade crítica. Portanto, a formulação deve equilibrar todos os aspectos [1].
Existem muitos outros polímeros usados na aplicação de dispositivos médicos além dos listados na tabela 1 e mais estão sendo desenvolvidos e usados a todo tempo [6].
Tabela 1 – Polímeros mais utilizados em dispositivos médicos.
Polímero | Abreviação |
Polietileno de alta densidade | PEAD |
Polipropileno | PP |
Poliestireno | PS |
Polietileno tereftalato | PET |
Poliácido láctico | PLA |
Policarbonato | PC |
Policloreto de vinila | PVC |
Polietersulfona | PES |
Polimetilmetacrilato | PMMA |
Poli (ácido Iáctico-co-glicólico) | PLGA |
Polisulfona | PSU |
Poli(éter-éter-cetona) | PEEK |
Poliuretano termoplástico | TPU |
Policaprolactona | PCL |
Fonte: Adaptada de McKEEN (2014).
Os custos e investimentos na fabricação
Existem poucos produtos de dispositivos médicos na indústria que possuem um baixo custo do material e do produto final, a fim de ser um produto viável. A ideia é levar esse custo como um investimento a longo prazo de uma ferramenta, visto que haverá um retorno significativo tanto pela qualidade, quanto pela eficiência do resultado. Se, por exemplo, utilizar um material com propriedades de temperatura mais altas, o tempo que leva para esterilizar o produto pode ser reduzido usando uma temperatura de esterilização mais alta e não afetar qualquer outro aspecto do produto, isso pode ser uma opção muito favorável. O período de tempo para esterilizar e fabricar o produto seria reduzido e a economia de custos seria significativa [7].
Qualquer material que pode ser oferecido a um fabricante de dispositivos que tem potencial para reduzir o custo de fabricação pode trazer uma vantagem para esse produto. Pode ser tão simples quanto uma injeção de mais fácil moldabilidade ou tempos de ciclo mais rápidos; tudo isso seria considerado um valioso investimento para qualificar um novo material para uso em uma produção de alto volume de longo prazo [7].
Sobre a autora
Cristiane Nayuni Wada é Mestre e Engenheira de Materiais formada pela Universidade Estadual de São Paulo e atualmente é aluna de Doutorado em Ciência e Engenharia de Materiais. Sua tese foca no desenvolvimento de implantes drug delivery para tratamento de câncer.
Para saber mais informações clique aqui.
Veja outros artigos escritos por Cristiane:
APLICAÇÕES DE SISTEMAS DE LIBERAÇÃO DE FÁRMACOS IMPLANTÁVEIS
REFERÊNCIAS
[1] ZEMA L., et al. Injection Molding and its application to drug delivery. Journal of Controlled Release, v. 159, p. 324–331, 2012.
[2] HARADA, J. Moldes para injeção de termoplásticos. Artliber, 2004.
[3] FERNANDES, C. et al. Modeling and Optimization of the Injection-Molding Process: A Review. Advances in Polymer Technology, v. 37, n. 2, p. 429–449, 2016.
[4] CAVALHEIRO, A. Z. Influência dos parâmetros de moldagem na estrutura e propriedades de peças de paredes espessas e finas de polipropileno isotático injetadas em moldes-protótipo fabricados por vazamento de resina epóxi. tese de doutorado. Universidade federal de santa catarina. Florianópolis. 2007.
[5] GALDAMEZ, E. V. C.; CARPINETTI, L. C. R. Aplicação das técnicas de planejamento e análise de experimentos no processo de injeção plástica. Gestão & Produção, v. 11, n. 1, p. 121–134, 2004.
[6] MCKEEN, L. W. Plastics Used in Medical Devices. Handbook of Polymer Applications in Medicine and Medical Devices, chapter 3, p. 21-53, 2014.
[7] CZUBA, L. Application of plastics in medical devices and equipment. handbook of polymer applications in medicine and medical devices, chapter 2, p. 9-19, 2014.